When I say more common, I mean the ones that I find most frequently in Spain, not only in my works, but also in the works that I see in the East of Spain.
I am going to comment on the types of reinforced concrete slabs with which I have worked lately, although before that I do think that a general classification should be made between two large groups of slabs, the unidirectional and the bidirectional.

Unidirectional slabs are those that need supports at two of their end beams, to transmit the loads of the slab through them to the columns and from there to the foundation.
Unlike unidirectional slabs, bidirectional slabs do not need supports at the ends to transmit the loads, rather the loads of the slab are transmitted in both directions, creating a grid, until they reach the columns.
I don't want to get too technical or theoretical, it's not the purpose of this post, but at least I wanted to make this great classification clear, which I think is important to understand the types of slabs I'm going to comment on.
Perhaps the unidirectional slab of joists and vaults is the one that has been used the most in residential construction in Spain.
As I mentioned in relation to the unidirectional slabs, they need to transmit the loads they receive on the beams from two of their opposite ends in order to direct said loads to the pillars and foundations through them. The joists, which are made of prefabricated concrete elements, with prestressed reinforcement, supported by the formwork of the beams to be concreted together and form a monolithic element, are responsible for this transmission of loads from the floor to the beams.

The concrete beams can be semi-resistant or self-resistant, the difference between them being the ability to withstand loads before being concreted and being integrated into the slab. The semi-resistant ones require lower propping until the slab has acquired all its resistance, while the self-resistant ones do not need this propping because they have sufficient bearing capacity from the time of their placement.
The latter are usually used in ground floor slabs to avoid leaving props lost under the slab (it is not possible to access the void under the slab to recover the props once concreted)
For the transmission of loads to be effective towards the beams, it is necessary that there is a connection between the joists and the main beams. On some occasions this connection is solved by inserting the joists into the beams and on others you can choose to place connectors that join both elements. These connectors are simple corrugated steel rods that are placed on the "sides" of the joists and inserted into the beams.
In the following image you can see those connectors, especially in the joist that you see on the bottom left (if you have a better photo of the use of connectors and you want to share it, I will be delighted, thanks)

The resistance of the floor is based almost entirely on the concrete joists, so the space between them is hardly relevant in terms of load-bearing capacity, so it is not necessary for there to be a complete concrete mass between two joists. If so, much of that concrete would not work structurally at all, so it would simply be adding its own weight to the structure. This is solved by placing lightening elements supported between two joists, in such a way that they prevent the part of the floor between joists that does not work, the one in the lower area, not to be made of concrete, but of a much lighter element without structural capacity. . These elements are the vaults.
The vaults are usually made of concrete, although they can also be made of ceramic material or polystyrene (the typical white ball cork), with which we can further lighten the weight of the slab.
Obviously all these elements, before becoming part of the already concreted structure, need to be supported by the wrought formwork in order to be assembled. The formwork can be complete boarding (the entire surface is a wooden "floor" on which you can walk to work on it assembling the slab) or it can be partial formwork, in which only the beam areas are formwork where the heads of the joists are supported and on these the vaults are supported.
These partial forms save a large amount of formwork wood, but require working from the lower floor with auxiliary means until a support surface is formed, which must also be protected to prevent falls between the joists.
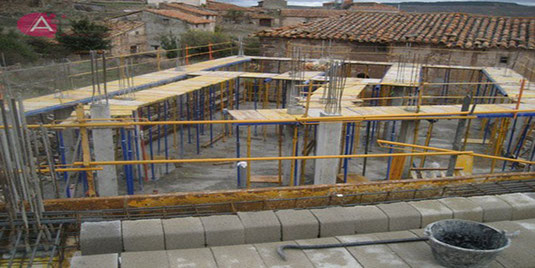
As I mentioned at the beginning, it is a fairly common type of forging, but it is not without some drawbacks. One of the main drawbacks of the unidirectional slabs of joists and vaults (hollow concrete or clay blocks) is that they require a large storage surface. The joists take up a lot, the vaults as well, the reinforcements, the formwork wood, the props etc they require having planned the space where all these materials are going to be stored in the work.
In addition, another drawback is that they are very heavy materials, which is why they require auxiliary means to take them to their place of placement, since it is not feasible for the operators to carry them to the corresponding plant by hand. Not only on a time issue, but for security.
In addition, all this weight affects the own weight of the slab, so the structure already needs a certain resistance to support itself, affecting the amount of concrete and steel that it will need by calculation.
Another drawback is the lack of flexibility with the geometry of the building floors. The joists cannot be cut on site as we please, so in the case of complex geometries in which the beams are not parallel (same distance between them, same length of all the joists), it would be necessary to order joists with different sizes to adapt its length to the geometry of the slab.

One-way forging of joists in situ
This would be a variant of the previous type of prestressed joist slab. In this type, the work system of the floor is the same, only instead of using prestressed joists (semi-resistant or self-resistant), these joists are assembled in situ during the assembly of the floor slab.
This is a great advantage for floors with complex geometries, since the dimensions of each of the joists can be adjusted to the centimetre, although it requires a more careful execution, since the main resistant element is not prefabricated (guarantee of correct manufacturing), but it can suffer execution failures during the process.
In addition to the joists not being a prefabricated element, the reinforcing reinforcement is not prestressed, so it has less resistance, which must be taken into account when calculating the structure.
Another factor to take into account is that, as they are joists executed in situ, greater care is required in the execution, both in the placement of their reinforcement elements, in terms of position, quantity and coatings, as well as in the concreting itself, which must be be vibrated even more carefully to guarantee a high-quality concrete that correctly resists the loads it has to bear and, above all, with the durability that is required of it.

Composite sheet metal slab
It is a type of slab that I had not worked with until now, but that I find very interesting in certain circumstances, such as metal structures.
In this type of structures, the collaborating sheet metal slab is very suitable, since the placement of joists and vaults is more complicated on metal profiles, so the use of sheet metal solves this problem. The truth is that I have not found any case of collaborating sheet placed in a concrete structure,
The sheet has folds executed that give it the shape of grooves, which once filled with concrete provide inertia to the element, also leaving the distribution of loads in one direction, so it would be a unidirectional slab.
As its name indicates, the sheet metal is a continuous element that collaborates by providing resistance to the slab, in addition to acting as formwork for it, which gives it a great advantage when it comes to its execution, since they are relatively light elements, quick to place and that when stacked they take up little storage space. In addition, except in cases of long spans, it is not necessary to prop up the slab, the sheet itself is self-supporting and does not need a support element during the hardening phase of the slab.

One of the great advantages of this type of slab is the speed of placing the plates. Being relatively large elements, the surfaces of the slabs are covered very quickly, allowing work on the sheet from the first moment without having to wait to have formwork or shoring in place, which is another advantage from the point of view of safety in site, since a safe working surface is formed while it is being assembled.
Being a type of slab that has a large part of its resistance from the first moment of concreting and as it does not need propping, the speed of execution is not only achieved by the preparation of the slab that is being executed, but also by the speed with which it can be used to build the next slab, without being conditioned, for example, by the number of propped-up floors.
Another advantage (in most cases) is the thickness of the floor. In the case of the work that I have executed, the total thickness of the slab has been 11cm (6+5), which compared to 30cm for most slabs is an important difference, especially if we are conditioned by the heights allowed by the planning.
Of course, it is a lighter slab than a traditional one with joists and vaults, with a lower volume of concrete (savings in material) and in the structure's own weight, which also produce savings in the calculation of, for example, the amount of concrete that required for the foundation.
But not all are advantages in the types of composite plate slabs, there are also some drawbacks.
The first of the drawbacks that everyone I talk to about collaborating sheet metal slabs mentions to me is the issue of fire resistance. As the sheet is a metallic element that collaborates with the resistance of the floor, it has fire resistance requirements that must be met, which can make the solution more expensive due to the fireproofing processes. from what I have been able to learn during the execution of this slab, it can be calculated against the action of fire by adding a certain amount of reinforcement to compensate for that risk. So this inconvenience does not seem so serious at first.
On the other hand, as it is a slab made up of two very different elements supported on a metallic structure that also have to collaborate with each other, it is necessary to place connection elements between them to make them work at the same time without producing grazing forces. These necessary elements are the connectors.

The connectors are elements that are inserted to the support element (beams) and that protrude from it to be embedded in the mass of the concrete, allowing the materials to deform over time, collaborating with each other without moving between them, which which would cause that, instead of working as a single slab, they would work as two slab placed one on top of the other, but without collaborating with each other.
For the execution of the collaborating sheet metal slab, despite being a simple and fast process, the use of nailing tools for the sheet metal against the metal structure is required, which can become an inconvenience, since it requires specialized equipment that must have control of the assembly team.
The placement of holes for the passage of slabs is also a bit complicated since, as it is not a flat surface but rather a corrugated surface, the placement of side shutter is complicated to leave these holes in the slab. It is not impossible, but it is a little more difficult than in a floor with a flat formwork surface.
The corrugated surface of the sheet metal also causes another inconvenience to be taken into account, since at the ends of the sheet metal, on its front, it is necessary to cover the holes that remain in the lower parts of the fretwork through which the concrete can be lost. . In certain points it will not be possible to place a plank that covers them all, but it will be necessary to "work" some more artisanal covers to solve this point.

I intend to prepare an article going much deeper into the use of the collaborating sheet metal slab type, so I refer you to keep an eye out for it to be prepared (I hope soon).
Forging of structural hollow bodies
The next type of floor slab that I want to talk to you about is the structural hollow body slab, which is being seen quite a bit lately, at least in the execution of single-family homes in Alicante and Murcia.
Actually, I should talk to you about the types of waffle or bidirectional slabs beforehand, but despite the fact that they are quite common. If you have had experience working with waffle slabs and you want to tell how it works, its advantages and disadvantages, I will be happy to insert your text here so that it can be of help to other colleagues.
For now, until some of you are encouraged to tell us about the use of waffle slabs, I'll stick to talking about my experience in the execution of hollow body slabs.
The slab of structural hollow bodies is a type of slab that works in a grid, as if it were a slab, that is, it does not need support elements at two of the opposite ends in the direction of the loads, but the forces are distributed in both directions until you find the supports. This already gives it an advantage in terms of the spans achieved between supports, which are usually greater in waffle slabs than in unidirectional ones, but which can also be further improved in the case of hollow body slabs thanks to the lower weight of the slab, since the neutral zone of the thickness of the slab is occupied by hollow "balls" of recycled plastic that hardly weigh anything and prevent their volume from being occupied by the concrete.

The carrying out of this type of slab is quite fast, since the hollow bodies are dropped onto a lower reinforcement of the slab, ordered according to the distribution of planes and attached at the top with the upper reinforcement. As the balls or cups (there are different formats) hardly weigh anything, they are placed very quickly and with hardly any effort to move them to the level of the slab.
The hollow bodies are made with recycled plastic, so another advantage of this type of slab is an environmental advantage, since it reuses plastics that were no longer going to be used and also greatly reduces the consumption of concrete and therefore the energy required for the manufacture of its components and their transport.
But the main advantage is the reduction of the structure's own weight without increasing the cost of the system used. In other systems that lighten the weight of the structure, the system itself is more expensive than a more traditional system of reinforced concrete joists and vaults, but by saving concrete thanks to a less demanding structure, the small additional cost of the system is compensated . However, the hollow body slab system is not more expensive to execute than one with joists and vaults, so it not only saves the additional cost of execution and the optimization of the amount of concrete required by calculation (less weight, less volume of foundation) but also the amount of concrete is saved thanks to the volume occupied by the hollow bodies (it is not occupied by the concrete).
On the drawbacks side, it should be mentioned that it requires a more specialized calculation. Its calculation is not standardized in the usual structural calculation applications, so it has to be calculated in a more "handmade" way. In the case of the house that I have executed with this system, the manufacturer of the hollow bodies himself has been in charge of carrying out the calculation of the structure that has later been incorporated into the project, it is clear that he has detected the inconvenience of the calculation, so he offers this service to the architects who prescribe it.
In terms of execution, it has the drawback that, being hollow balls with a certain volume, they tend to float when the concrete is poured, so a specific pouring procedure must be followed and the reinforcements must be prepared to hold the balls. in your position.
To prevent the balls from floating during the pouring of the concrete, the reinforcements must be fastened to the formwork, so that when the balls remain between both layers of reinforcement they no longer move. To fasten the reinforcement to the formwork, care must be taken to place flanges attached to the formwork girders, protruding from the upper face of the formwork. These zip ties will then be used to tie to the bottom grill of the slab.
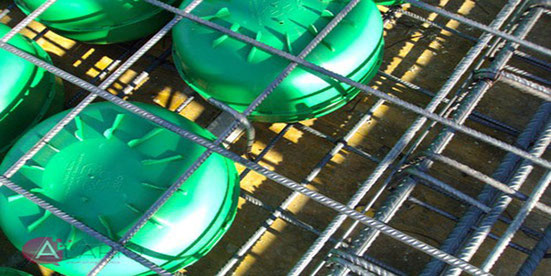
Once we have the lower grill attached, the balls are placed on it and then the upper grill. So that the balls do not lift the upper grill when it floats with the concrete pouring, it is attached to the lower grill (attached to the formwork with the flanges) by means of hooks that join both grills.
As I intend to make a more in-depth post on this type of slab, I will tell you about it in greater detail, since the objective of this post is simply to show you the most common types of slabs in construction and I think I have fulfilled that.
It is possible that you have left me one that you consider habitual, or that is often used in the area where you work, so do not hesitate to tell me and if you dare, tell us about your experience with that type of slab that I have not worked with. still but that you do control.
I hope you liked the post, if so, do not hesitate to share it with your contacts on social networks, perhaps they will also be interested.
Here at Pacheco & Asociados Architects we have more than 25 years of experience in dealing with these types of concrete slabs in the regions of Murcia and Alicante.
Write a comment